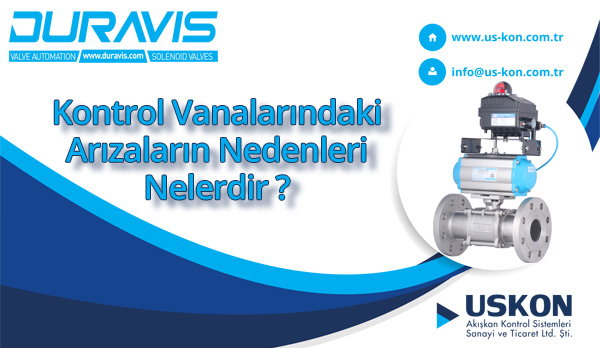
Kontrol vanaları arızaları ve temel nedenlerin anlaşılması çok zor bir iş olabilmektedir. Bu konudan bahsetmeden önce, kontrol vanalarının temellerine değinmek önemlidir. Kontrol vanalarının arızalarını gidermek, kontrol devresinin performansını ciddi şekilde etkiler. Bazı kontrol vanaları arızaları, deneyimli kontrol vana teknisyenleri için oldukça açıktır ve bu arızalar, performans değerlendirme yazılımları tarafından kolaylıkla tespit edilebilir. Diğerleri, belirli testleri yapmadan algılanması daha zor olabilmektedir. Kontrol vanaları ile en büyük zorluklardan biri, yerinde servis isteği ile arıza analizi ve vana değişimidir. Bu nedenle, aşağıdaki vana problemlerine dikkat etmeyi ve / veya denediğimizden emin olmamız gerekmektedir.
Kontrol vanaları ile ilişkili beş ana hata koduna, düşük performans gösteren kontrol döngüsünde sıklıkla rastlanır. Bunlar; ölü bant, yapışma (statik sürtünme), pozisyoner ayar bozulması, yanlış vana boyutlandırma ve doğrusal olmayan akış karakteristikleri gibi unsurlardır. Şimdi bu sorunların her birine bir göz atalım.
Ölü Bant
Ölü bantlı bir valf, kontrolör çıkışı ile gerçek valf konumu arasında bir ölü nokta varmış gibi davranır. Dolayısıyla bir gecikme sözkonusudur. Kontrolör çıkışının yönü her değiştirildiğinde, valf fiziksel olarak hareket etmeden önce ölü bandın geçilmesi gerekir. Ölü bant, mekanik geri tepmeden (gevşeklik veya mekanik bağlantılarda oynama) kaynaklanabilse de, valfdeki aşırı sürtünme, olması gerekenden daha küçük bir aktüatör veya bozuk bir pozisyonerden de kaynaklanabilir. Ölü bantlı bir kontrol valfı, kontrolör doğrudan kontrol valfini (ardışık olmayan) sürerse PI veya PID kontrolü altındaki seviye döngüsünde salınımlara neden olur. Ölü bantlı bir kontrol valfı, kendinden regülasyonlu işlemlerde kontrol döngülerindeki ayar noktasının değişmesinden sonra salınımlara neden olabilir. (Özellikle de kontrolörün integral hareketi biraz aşırı ise)
Yapışma/Sıkışma (Statik Sürtünme)
Kontrol döngülerinde bulunan bir diğer yaygın problem, yapışmadır. Bu durum statik sürtünme olarakta adlandırılır ve vana iç parçalarının yapışkan olduğunu gösterir. Yapışkan bir vana parçası hareket etmeyi bırakırsa, o konuma yapışmaya eğilim gösterir. Bu tutukluğun üstesinden gelmek için ek bir kuvvet gerekir. Kontrol cihazı, valf bu haldeyken, çıkışını değiştirmeye devam eder. Aktüatörde ilave basınç gönderilir. Statik sürtünmeyi aşmak için yeterli basıncın üzerine çıkılırsa, valf hareket eder. Valf hareketi basınç fazlalığını hızla absorbe eder ve genellikle valf hedef pozisyonunu aşar. Bundan sonra, valf hareketi durur ve valf yeni konuma yapışır. Sıklıkla, valf konumundaki bu aşma, prosesin ayar noktasını aşmasına neden olur. Daha sonra valf yeni konuma yapışır, kontrolör çıkışı yön değiştirir ve tüm işlem ters yönde tekrarlanır. Bu, tutma-bırakma döngüsü bir salınmaya neden olur. Döngü salınımları yapışma nedeniyle oluyorsa, proses değişkeni bir kare dalga veya düzensiz bir sinüs dalgası gibi görünebilirken, kontrolör çıkışının çevrimi çoğu zaman bir testere diş dalgasına benzer. Bu sıkışma; aşırı-sıkı vana mil ringleri, yapışkan valf iç parçaları, küçük seçilmiş aktüatör veya yapışkan bir pozisyoner neden olabilir.
Pozisyoner Aşımı
On yıl öncesine göre şimdi daha yaygın olan kontrol vanası problemlerinden biri de; pozisyoner aşımıdır. Pozisyonerler, vana (stroke) konumunu ölçen ve vana istenen konuma gelene kadar aktüatörünü yönlendiren hızlı geri beslemeli kontrolörlerdir. Çoğu pozisyoner ayarlanabilir. Bazıları kontrol ettiği vanaya göre çok agresif ayarlanmış olabilir. Bu da, kontrolcü çıkışı değiştiğinde vananın hedef konumunu aşmasına sebep olur. Bazen pozisyonerler bu şekilde bir aşmaya sebep olacak şekilde arızalı da olabilir. Eğer proses kontrolcüsü de agresif şekilde ayarlandı ise poziyonerdeki bu sorun ile birleştiğinde kontrol loop’unda ciddi bir salınıma sebep olabilir.
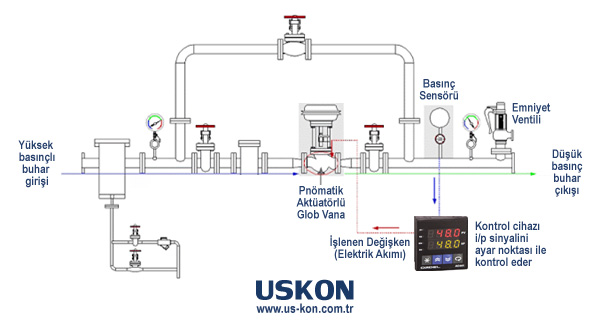
Vana Boyutlandırma
Kontrol vanaları ile ilgili dördüncü problem vananın büyük boyutlandırılmasıdır. Vana, servis koşullarına ve vana karakteristik eğrisine bağlı kalmak şartı ile akış değerini %70-%90 hareket ile sağlayabilmelidir. Çoğu durumda vanalar, kontrol ettikleri akış oranına göre büyük boyutlandırılır. Bu da akış maksimumda olduğunda dahi vananın küçük hareketler ile çalışmasına sebep olur. Vana pozisyonundaki küçük bir değişiklik akış üzerinde büyük bir etki oluşturur. Kontrol loop performansını olumsuz etkileyen ölü bant ve sıkışma gibi vana pozisyonlama hataları, büyük boyutlandırılmış vanalarda daha da fazla büyür.
Doğrusalsızlık (Non-Linearity)
Doğrusal olmayan akış özelliğine sahip bir valf de ayar problemlerine neden olabilir. Bir kontrol vanasının akış karakteristiği, normal servis koşullarında valf konumu ve valf içerisindeki debi arasındaki ilişkidir. İdeal olarak akış karakteristiği doğrusal olmalıdır. Doğrusal olmayan bir özellik ile, sadece bir çalışma noktasında en iyi kontrolör tepkisine sahip olabilir. Valf konumu bu çalışma noktasından uzaklaştıkça, döngü oldukça dengesizleşebilir veya durgunlaşabilir.
Sonuç
Bu nedenle, bir kontrol döngüsü ayarlamaya çalışmadan önce kontrol valfi arızasının nedenlerini saptamak önemlidir. Valfi ölü bant için kontrol etmek, sıkışma/yapışmayı ve doğrusalsızlık varsa belirlemek bize, döngü ayarlama çabalarından saatlerce tasarruf sağlayabilir.
Daha fazla bilgi için;
www.duravis.com
www.us-kon.com.tr